Noticias
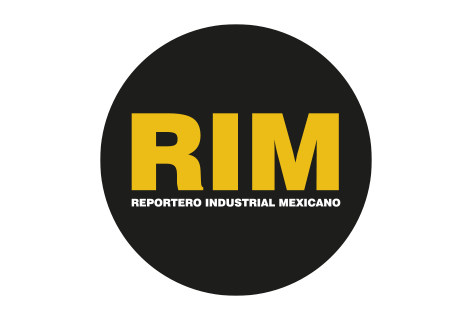
Los fabricantes de vehículos eléctricos (VE) deben producir transmisiones más livianas y compactas a partir de materiales resistentes, como aceros de baja aleación, y aquellos que dependen de procesos de manufactura tradicionales corren el riesgo de quedarse atrás.
Las ventas de vehículos eléctricos (VE) han dado un gran salto en los últimos años. De acuerdo con los Volúmenes de VE, en febrero de 2022 se registraron en todo el mundo 541,780 autos eléctricos enchufables nuevos, el doble que en febrero del año anterior. Este mercado creará un campo de juego diverso y competitivo, ya que compañías más grandes y establecidas, como Porsche, compiten con fabricantes más pequeños y en expansión global, como Polestar.
La fabricación de vehículos eléctricos también presentará desafíos adicionales, algunos de ellos relacionados con la dependencia de procesos de producción tradicionales. Para examinar estos desafíos, centrémonos en la fabricación de componentes de engranes.
La capacidad de controlar las revoluciones por minuto (rpm) de un engranaje es esencial para todo tipo de vehículos, incluidos los vehículos eléctricos. Todas las transmisiones de los VE son lo que se llama transmisiones reductoras, diseñadas con el fin de disminuir la velocidad del vehículo para que pueda controlarse y conducirse económicamente.
Debido a que no hay ruido de motor de combustión en un VE, se notará cualquier ruido que haga la transmisión. Por lo tanto, el principal objetivo es evitar el ruido.
Aquí es donde la calidad de la configuración del mecanizado juega un papel decisivo para que la transmisión sea lo más compacta, ligera y silenciosa posible. Las transmisiones de los VE suelen tener un diseño planetario, con los engranes planetarios y el engranaje central ensamblados dentro de la corona dentada periférica para obtener un conjunto compacto y liviano.
Lea también: Eliminar el Cuello de Botella en maquinado de alta
velocidad
La corona dentada es el componente más difícil de producir debido a sus paredes delgadas y sus estrictas tolerancias de redondez. Desafortunadamente, los procesos de fabricación tradicionales pueden agravar estos problemas con impactos negativos tanto en el tiempo como en el costo.
Los procesos de manufactura tradicionales por lo general se basan en máquinas de un solo propósito. Cada máquina está limitada a un área determinada de mecanizado, y se pasa la pieza de trabajo de una máquina a la siguiente. Esto hace que las líneas de producción sean inflexibles en términos de responder a cambios en diseño.
Trasladar la pieza de trabajo de una máquina a otra también puede afectar la calidad del componente con desviaciones del centro. El tratamiento posterior al calor es más difícil de controlar, y los métodos tradicionales de mecanizado suave seguidos de procesos de esmerilado son muy costosos. Estos procesos también requieren mecanizado adicional con aceite para mejorar los procesos de mecanizado y evacuación de virutas.
Las máquinas de un solo propósito perderán sus ventajas a medida que la flexibilidad, la productividad y la rentabilidad se vuelvan más importantes para la fabricación de piezas de vehículos eléctricos, de ahí la importancia de incrementar la base instalada multitarea.
Un equipo de esmerilado comúnmente utilizado en la fabricación tradicional puede ser una inversión costosa y una buena manera de evitar esto es dividir el mecanizado de componentes de engranes en dos procesos: mecanizado suave y duro, lo cual se puede realizar con una única configuración de máquina multitarea.
Estos equipos pueden eliminar procesos de maquinado, así como el tiempo y costo asociados a ellos, y con ello mejorar la calidad de la pieza. Además, junto con las mejoras en la calidad del producto, los tiempos del ciclo del proceso son mejores, o por lo menos iguales, que las soluciones de producción existentes. De hecho, datos obtenidos por el fabricante de herramientas Sandvik Coromant muestran reducciones de costos de hasta 30% para el usuario final.
Lea también: Las historias que cuentan los datos
El power skiving se puede aplicar tanto a engranes y estrías internas como externas, pero es especialmente productivo cuando se trata de mecanizado interno. Este método funciona particularmente bien en la producción en serie, en la que los plazos de entrega cortos son vitales.
La corona dentada es el componente más difícil de producir en un engranaje planetario, pero el concepto de power skiving, que en realidad existe desde hace más de un siglo, está emergiendo como la forma más eficiente de lograrlo. Se trata de un proceso que fusiona la conformación y el troquelado (un proceso de mecanizado para el corte de engranes) en un proceso único de corte continuo.
Esto tiene varias ventajas significativas respecto a los métodos de mecanizado tradicionales. En lugar de depender de una máquina de un solo propósito, con el power skiving se puede mecanizar un componente completo en una máquina multitarea para una mayor productividad y flexibilidad. No hay necesidad de máquinas especializadas y pueden eliminarse por completo las restricciones en la calidad debidas a los cambios de máquina. Esto reduce significativamente el tiempo total de producción en comparación con los procesos que implican fresado, conformado y troquelado, para un mecanizado de componentes más manejable y predecible.
El power skiving es cada vez más popular, y se han entregado más de 700 herramientas de power skiving desde 2014. La mayoría de estas, más del 60%, son máquinas multitarea. Esto significa que los principales procesos de mecanizado se realizan dentro de la misma configuración única, lo cual mejora la calidad de los componentes y permite un mecanizado más eficiente.
Las herramientas para este tipo de maquinados requieren ciertas características especiales y de alta gama. Ejemplo de ellas es la CoroMill® 178, un cortador de power skiving sólido que se puede pedir como acero de alta velocidad de polvo metalúrgico (PM-HSS ) o carburo sólido.
Las herramientas se pueden optimizar en términos de rigidez y voladizo, suministro de refrigerante y máxima vida útil de la herramienta. Esta combinación de factores asegura una producción confiable las 24 horas. Usuarios de estas herramientas han reportado reducciones de hasta 90%, sin contar el incremento de la vida útil de la herramienta.
Procesos como el power skiving está emergiendo como métodos de rápido crecimiento para el mecanizado de engranes y se suma a la oferta de nuevas tecnologías y técnicas que respaldarán el crecimiento de la industria de EV.
Otros artículos de interés
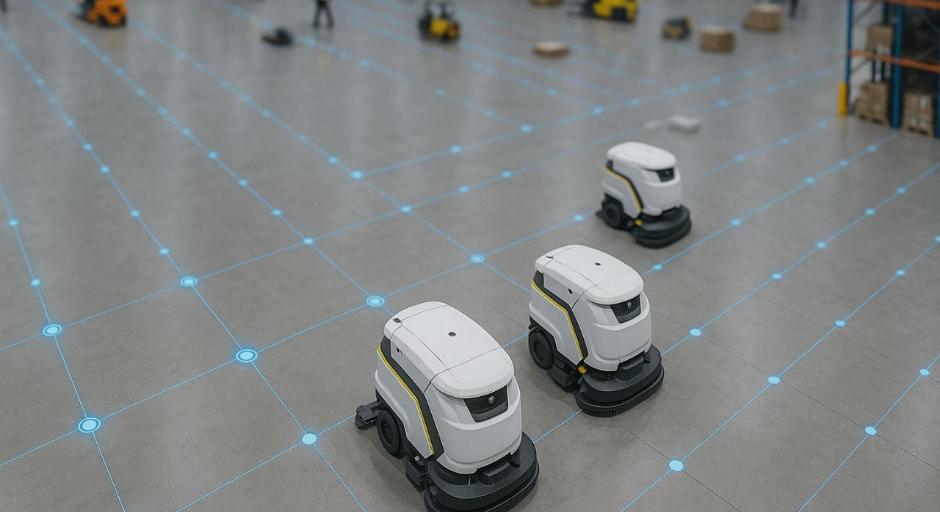
Limpieza industrial no escapa de la automatización
En la industria, la limpieza de áreas productivas es tan importante como
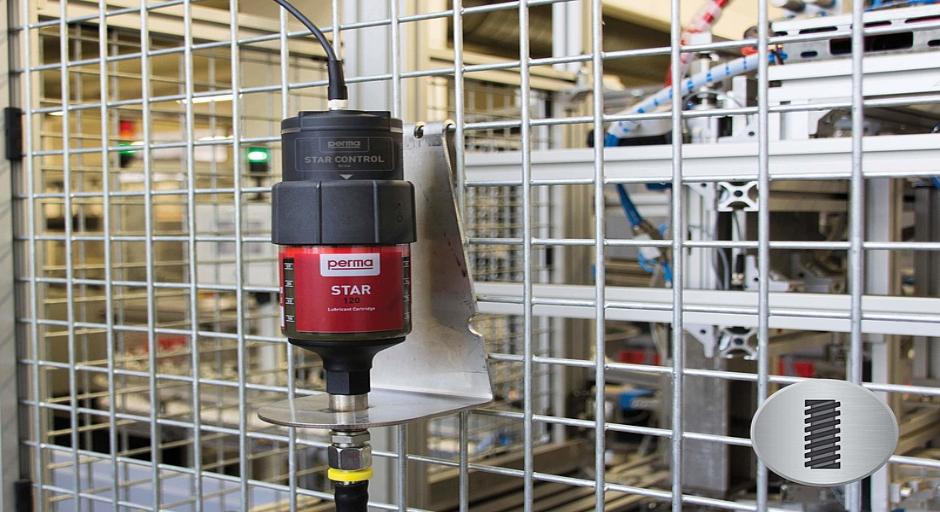
Lubricación automatizada, paso obligado en operación: Perma
En las plantas industriales, la lubricación ha pasado de ser una rutina

Suministro ininterrumpido para la Industria 4.0
La Industria 4.0 representa un salto evolutivo en la manufactura: sistemas físicos,
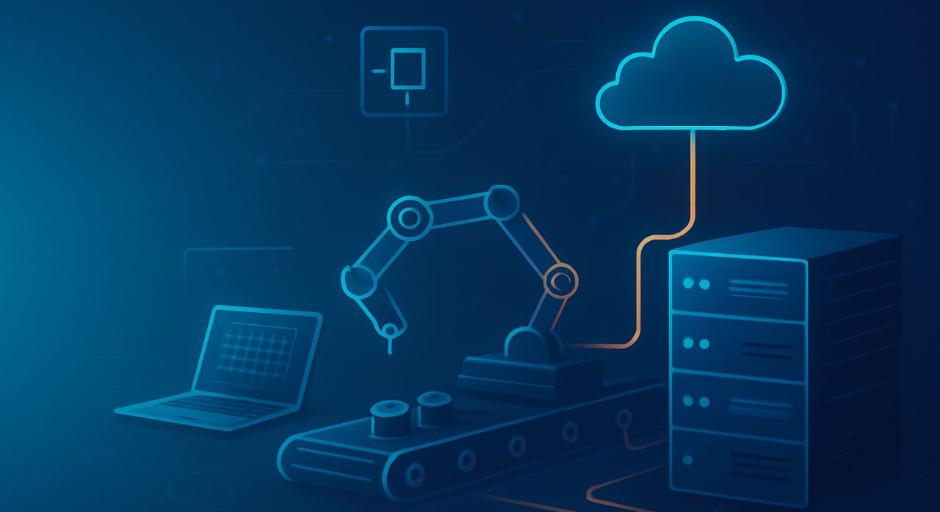
Por qué la manufactura requiere una buena infraestructura de redes
Con la adopción de tecnologías digitales en la manufactura, la infraestructura de

Transporte multimodal gana valor en la industria
En la industria manufacturera mexicana, la logística ha dejado de ser un
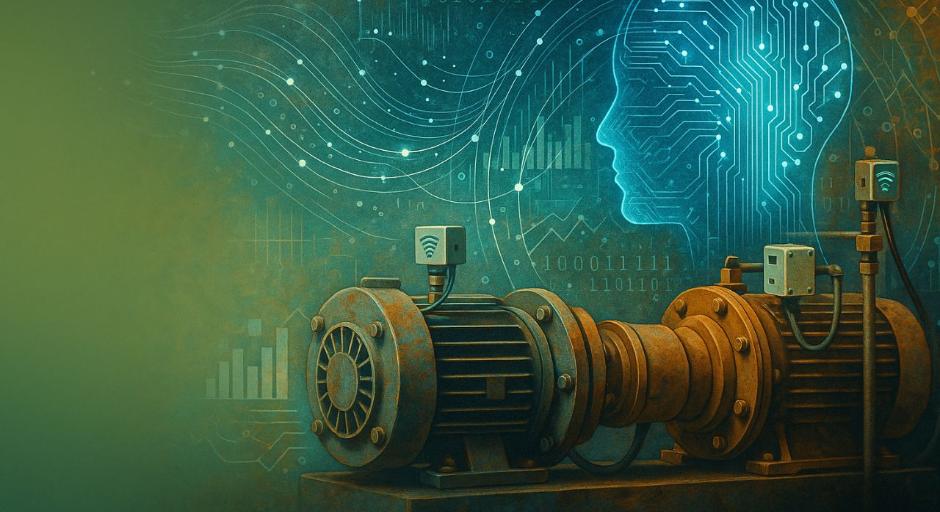
El uso adecuado del IIoT tiene impacto positivo en predictivos
El uso de sensores y sistemas conectados es cada vez más profundo